
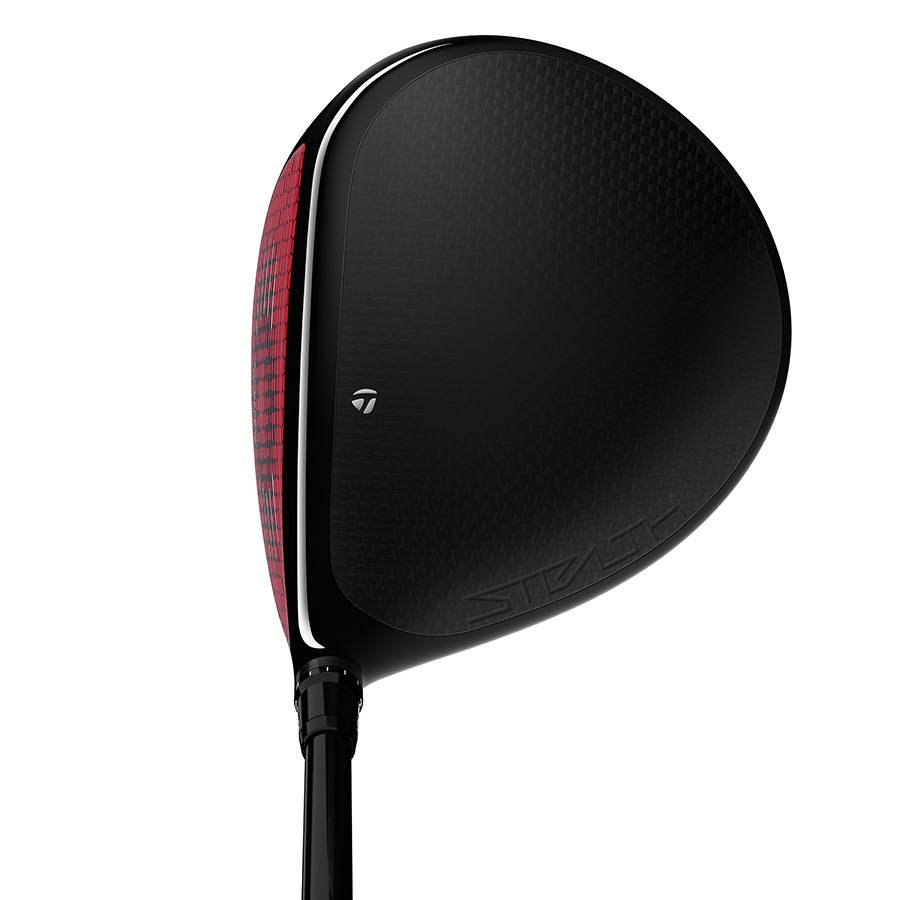
To allow the CNC machines to reach the bottom of its faces, TaylorMade had to give up its weight track.īy my recollection, every flagship TaylorMade driver going back to R5 TP has featured some sort of movable weight technology. While all of this sounds great so far, sacrifices had to be made to the driver design gods. TaylorMade, however, says the added precision provided by CNC milling allows for tighter controls which, in turn, give it the ability to manage speed (technically CT) from a single toe port. That intelligent optimization stuff allows TaylorMade to reduce the number of Speed Injection ports from two on the face to a single port in the toe.īased on the count alone, that would seem to limit TaylorMade’s ability to precisely position its speed-reducing goo (the idea of Speed Injection is to manufacture faces faster than they’re allowed to be and then add the amount of material necessary to slow them down to levels the USGA finds acceptable). A bit like COBRA’s e9 face, the idea is an elliptical pattern where speed is boosted in high-probability impact zones like the high toe and low heel areas. Ultimately, the speed story boils down to using CNC milling to precisely control face thickness with an eye for maximizing speed in the areas where golfers most commonly make contact.
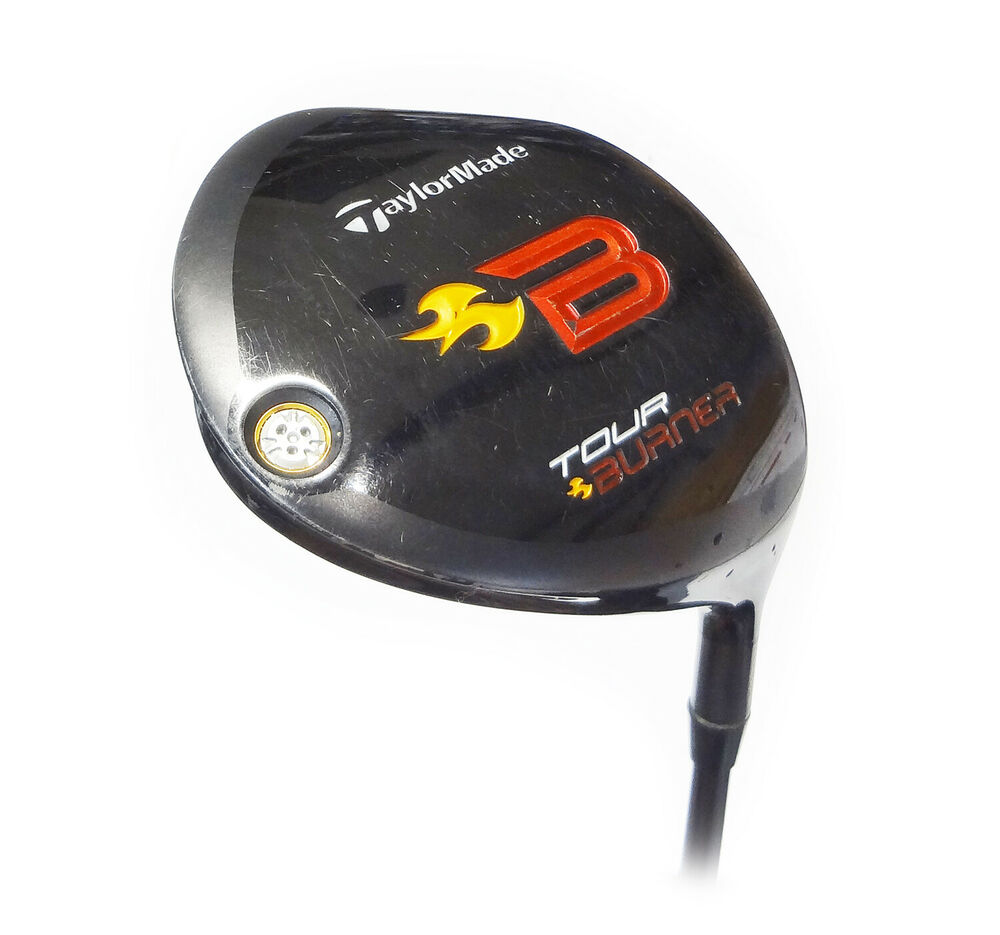
The benefit is more speed over a larger portion of the face. 800) on the SIM2 driver is 43-percent larger than on SIM.
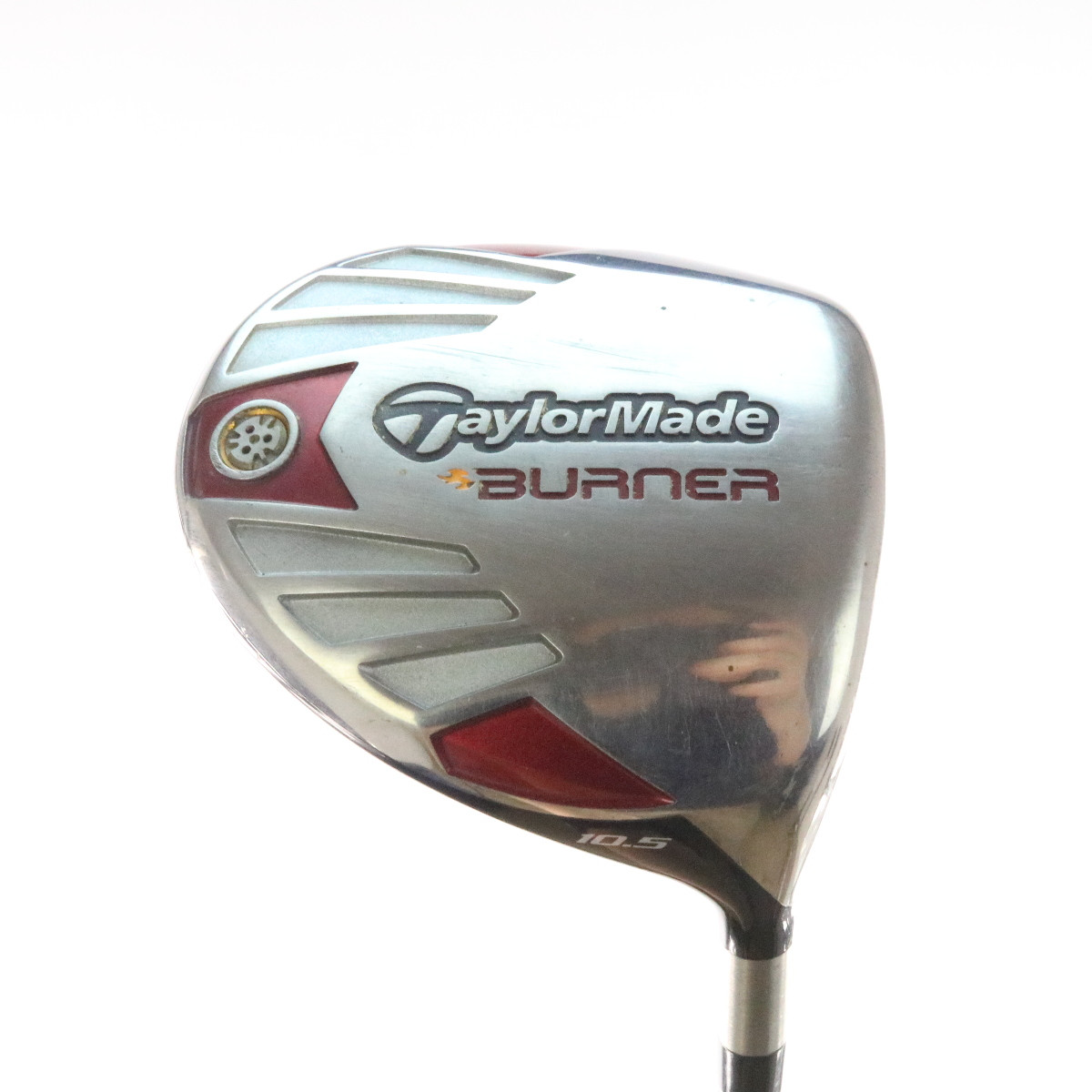
The milling allows for what TaylorMade calls an “intelligently optimized sweet spot.” By the numbers, the sweet area (the part of the face where COR is at least. COBRA does it on the outside, TaylorMade does its milling on the inside. If you look closely enough at the inside (you shouldn’t because you’ll have to destroy your driver to do it), you can see the critical detail that drives this story - a CNC-milled face design. The entire front portion of its driver - face, ledges for the crown and sole, cut-through slot, front swingweight port, hosel - basically all the business at the face end is made from a single piece of titanium. With the TaylorMade SIM2 Driver, the company is taking a different, perhaps more aggressive, approach. As you may know, the imprecision of the polishing process is the reason why COBRA CNC mills the exterior of its driver faces. Polishing isn’t entirely precise and can impact things like loft, bulge and roll as well as general consistency from one driver head to the next. The weld marks are then polished (ground) and, yeah, that’s pretty much it. With a unique combination of titanium, carbon fiber, aluminum and, if you want to count the rear-mounted weights, tungsten or steel depending on the model, the TaylorMade SIM2 driver is serving up a new level of multi-material construction.Ī quick refresher: the majority of driver designs feature an elliptically shaped face insert that’s, well, inserted into an opening in the chassis and then welded into place. TaylorMade believes it has succeeded and has Voltroned the parts of the SIM2 driver into a singular better whole that provides quantifiable performance improvements over the first iteration of SIM. In designing the SIM2 driver, TaylorMade considered the face, sole, crown and skirt and looked for ways to improve each part individually. In simple terms, it means an examination of each of the various pieces of the SIM2 driver as truly individual components.
#Taylormade driver burner series drivers
The company describes its methods as rethinking how drivers are built from ground up. Just as with the larger story, TaylorMade’s approach is the same … but different. In my story on the G425 drivers, I wrote about PING’s pursuit of small improvements with the hope that chaining enough of them together will lead to a quantifiable improvement for most golfers.
